Some of you who know me personally, know 1 of the business I own is a powder coating shop (Gemtech).? Since it's a coating business, we've dealt with alot?of surface finishes and finish removals.? Following are a few?airsoft/surface finishing?related?things
Powder Coating
Powder coating is a process where a dry powdered paint is baked?onto a metal surface (Or any surface that can withstand 400? F Temps).? The advantages are it's extreme durability, flexibility, corrosion protection and an environmentally safe process?when compared to a wet coating. But with products with tight tolerances, such as firearms, the coatings are too thick, unless engineered to be powder coated.? Since it is based on a heat process, powder coating is typically NOT used in real firearms (Most firearms will exceed 400? F Temps, and the powder coat will start to soften)?.
Contrary to popular belief, most airsoft metal parts (i.e. slides, bodies, etc)?coming out of China are NOT powder coated.? This is mainly due to cost and there's no need for powder coating's?durability.? Asia does not have to deal with EPA (Environmental Protection Agency), like here in the U.S., so a process like powder coating, would just result in added cost.? If you come across any paint that seems a little thicker and tougher to remove, it's probably an automotive based wet paint.?There are a few other coatings buzz words people may use, Cerakote,?Gunkote, Parkerizing and Anodizing.? These are all wet coats or metallurgical processes and not Powder Coating.
Way's to tell if an item is truly powder coated:
- The finish will NOT be smooth, It will have an "Orange Peel" texture.
- Where metal to metal parts meet, it should be devoid of any coatings.? Powder coating adds at least 2mil/inch per coat, which in layman?s terms means moving parts will stick.
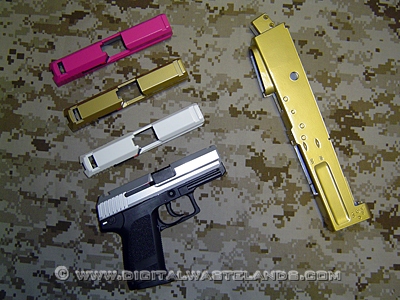
USP Compact Slides and AK47 Metal Body
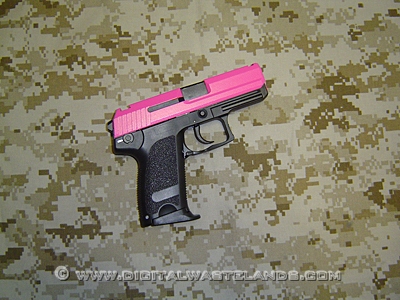
USP Compact Slide Hot Pink – For the Ladies… Seriously… 😉
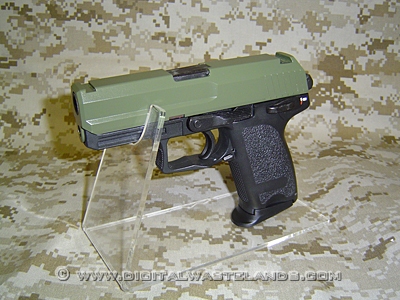
USP Compact Slide Olive Drab
Back to Top
Laser Etching/Engraving
A few years ago, we pulled in the capability of laser etching/engraving. In the following examples, the laser was used to burn off just the surface powder coat, thus creating an engraved effect. While the end results look great, the process is relatively expensive.
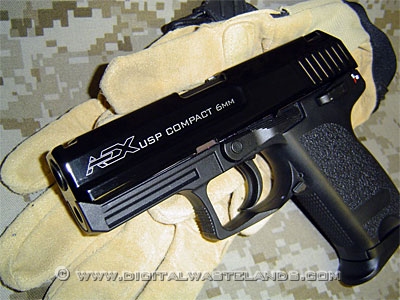
USP Compact with Powder Coated and Laser Etched Slide
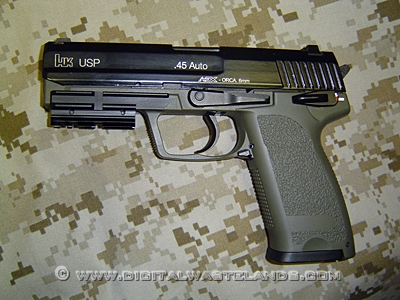
USP Full Size with Powder Coated and Laser Etched Slide
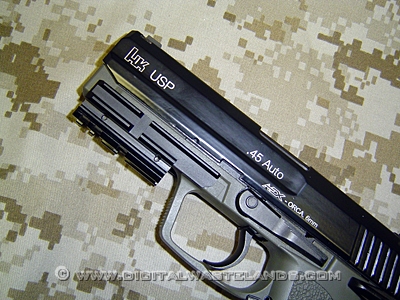
USP Full Size with Powder Coated and Laser Etched Slide. Close up
Back to Top